Quality Control Magnetic Whiteboard Systems
Total Quality Management Boards for Lean Manufacturing
When you display goals, standards, issues, improvement and performance data with our quality control boards, work associates, teams, and departments become engaged and stay focused on quality ownership.
These board systems were created from suggestions by our 5S lean manufacturing customers and are the boards they tell us have been most successful. 5s methodology makes workplaces cleaner, more efficient, faster, and safer.
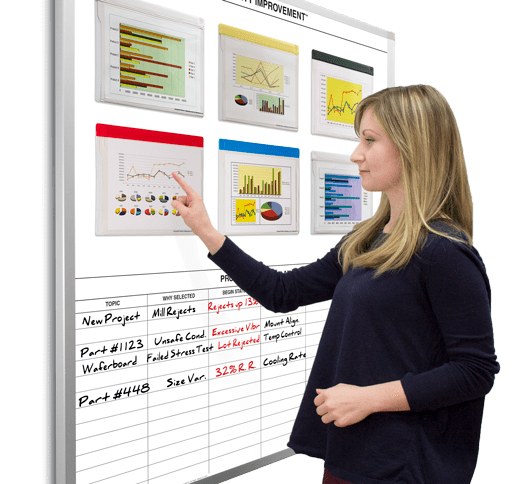