Magnatag InSight
The whiteboard and how it helps us brainstorm, innovate, motivate and create
How do Lean Manufacturers/Distribution and Warehousing companies use Kanban boards for Job Loading and Inventory Management?
Thu Nov 14 2013Kanban is a lean production technique for inventory management and job loading that is fundamental to streamlining the flow of work to meet customer demands. Even though electronic Kanban and inventory management systems are becoming more robust, basic analog kanban card systems continue to provide a quick and easy alternative. Based on our experience with customers who use these boards every day, here are some examples of effective implementation.
Understanding the Kanban card
Each Kanban card represents either one unit of material to be consumed during production or one unit of product to be produced. Kanban cards can be as simple as a printed 3x5" card with handwritten information about the items they represent including part number, quantity to make or supplier, color, size and other specifications. Or they can be more complex and include bar code, routing, sub-assembly and quality standards. The best configuration for each card is determined by the complexity of the product.
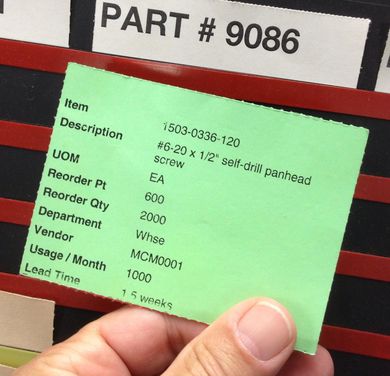
With Kanban, facilities stock inventory based on orders placed by customers instead of forecasts. As new orders come in and material is used the cards generate a replenishment signal for purchasing to reorder from suppliers.
The Inventory On-Hand Board
As a batch of materials are used, associates remove the corresponding Kanban card from their inventory on hand board and hand it off to a manager who is responsible for replenishment.
Using the K.I.S.S. principal, yellow and red tapes are placed on the board at predetermined reorder points and visually communicate low inventory levels to associates and management.
The Next-Job Kanban Board
The Kanban cards on this board represent jobs to be done or orders to fill and show an operator what job to do next. In this case the cards are arranged in columns under each part number.
Red and yellow tapes placed under each part number communicate which parts need to be done first. Operators have the flexibility to fill orders based on demand and can take into account the most efficient way to manage machine set up and change over to produce the product required.
The benefits of Kanban in a lean environment include:
- Less inventory on hand
- Lower inventory costs
- Improved machine utilization
- Faster through put
- Improved material flow
- Smaller amount of work in progress
Click here to see additional Kanban Visible Job Card systems including Load Leveling, Do-Done, Build-Boards and Job-Load boards.