Magnatag InSight
The whiteboard and how it helps us brainstorm, innovate, motivate and create
The 5 Lean Principles: What You Need to Know About Lean
Fri May 1 2015By: Victoria Burns
History of Lean Principles and Lean Manufacturing
Lean is a method for eliminating waste in a manufacturing environment. It focuses on eliminating the 3Ms of waste: Mura, Muda and Muri. The lean manufacturing philosophy created mostly from the Toyota Production System. John Krafick, a former quality engineer in the Toyota-GM NUMMI joint venture, brought the term “lean principles” to the United States from the Japanese manufacturing industry. There are now five lean principles that are used to guide lean techniques and make the lean manufacturing environment successful.
There are two different approaches to lean, although the overall goal for both of them is to eliminate waste:
Five Lean Principles
Lean manufacturing implements principles, tools and techniques that focus on eliminating waste and manufacturing more products with less material. There are five key principles of lean that guide the execution of lean techniques and 6 lean manufacturing tools that most aren’t utilizing, but should consider putting into place in their lean manufacturing practices. Lean principles are executed in many industries including manufacturing, hospitals, financial, technical, engineering and several others.
The five key principles include:
Basic Concept of Eliminating Waste and the Types of Waste
The Toyota Production System views the waste elimination as a method of eliminating the 3Ms:
The last type of waste is Muri, which is the waste of overburden. The waste of overburden happens by putting unnecessary stress on employees and the processes they perform. An example of Muri waste would be lack of training employees or when employees use of the wrong tools.
Magnatag Visible Systems develops ready-to-use whiteboard systems specifically for companies who practice lean manufacturing. For more information about the products, visit www.magnatag.com/factory or call a Visible Systems Specialist at 1-800-624-4154.
Resources:
Lean is a method for eliminating waste in a manufacturing environment. It focuses on eliminating the 3Ms of waste: Mura, Muda and Muri. The lean manufacturing philosophy created mostly from the Toyota Production System. John Krafick, a former quality engineer in the Toyota-GM NUMMI joint venture, brought the term “lean principles” to the United States from the Japanese manufacturing industry. There are now five lean principles that are used to guide lean techniques and make the lean manufacturing environment successful.
There are two different approaches to lean, although the overall goal for both of them is to eliminate waste:
- Lean: the smooth flow system takes into account a system-wide perspective and waste is naturally reduced.
- Toyota Production System: This system eliminates all waste and assumes it will help the system.
Five Lean Principles
Lean manufacturing implements principles, tools and techniques that focus on eliminating waste and manufacturing more products with less material. There are five key principles of lean that guide the execution of lean techniques and 6 lean manufacturing tools that most aren’t utilizing, but should consider putting into place in their lean manufacturing practices. Lean principles are executed in many industries including manufacturing, hospitals, financial, technical, engineering and several others.
The five key principles include:
- Value: Creating products that fulfill customers’ needs
- Value Stream: Identifying steps for manufacturing process and eliminating the steps that don’t add value to create the value stream
- Flow: Creating a workflow system so the customer gets the product without interruption, delay or damages.
- Pull: Supplying what is demanded. Pull (produce) only when the customer pulls (orders).
- Perfection: Reaching for perfection and continue eliminating waste as issues arise.
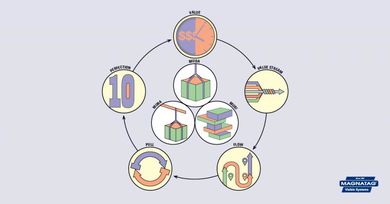
Basic Concept of Eliminating Waste and the Types of Waste
The Toyota Production System views the waste elimination as a method of eliminating the 3Ms:
- Muda (waste)
- Mura (waste created through unevenness)
- Muri (waste created through overburden)
- Transport: products that are moved that aren’t required to perform processing
- Inventory: including all materials, work in process and finished products not being processed
- Motion: employees/equipment moving more than is required to perform processing
- Waiting: Shift change interruptions of production, waiting for the next production step
- Overproduction: Producing before/more than is demanded
- Over Processing: Working on products more than necessary
- Defects: The effort it takes to inspect and fix defects
The last type of waste is Muri, which is the waste of overburden. The waste of overburden happens by putting unnecessary stress on employees and the processes they perform. An example of Muri waste would be lack of training employees or when employees use of the wrong tools.
Magnatag Visible Systems develops ready-to-use whiteboard systems specifically for companies who practice lean manufacturing. For more information about the products, visit www.magnatag.com/factory or call a Visible Systems Specialist at 1-800-624-4154.
Resources:
Categories:Factory and Production