Magnatag InSight
The whiteboard and how it helps us brainstorm, innovate, motivate and create
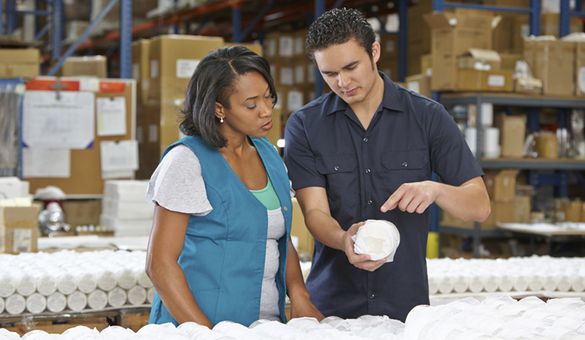
What you Need To Know About Your Lean & Agile Manufacturing Efforts
Tue Apr 5 2016By: Mike P
The demand from consumers for new products with customized options has never been greater. As a result, the manufacturing marketplace has become extremely volatile, with new technologies and methods arising every year. Over the past decade, many manufacturing managers have adopted a Lean process as the standardized method for organizing their factory workflows.
What originally started in the world of software development as a way to keep up with ever-changing customer needs and irregular product development cycles, Agile manufacturing has recently become a go to method for product design and development processing. The topical debate between Agile and Lean production methods has taken on a greater importance to North American manufacturers, as many industry experts have been begging the question of whether or not Agile production methods can truly be seen as an evolutionary step forward for production processing.
It is easy to understand why the agile manufacturing process may be appealing to some companies: it gives you an advantage when dealing with customer requirements, while giving you a competitive edge in an ever-evolving marketplace.
Agile methodologies can be viewed as an alternative to sequential design processes, providing manufacturers with the ability to act quickly upon unforeseen events and customer demands. With a successful Agile strategy, companies can become more dynamic, adding increased product variations and shorted lead-times.
On paper agile manufacturing sounds like a no brainer for consumer-driven manufacturing facilities, but what goes into making a facility like this run smoothly?
There are four key elements to agile manufacturing, all of which, will peak the curiosity of any Lean enthusiast:
So perhaps rather than looking at Agile methodologies as a different way for production facilities to implement rigorous change, factory managers should begin taking queues from the Agile process in an effort to evolve their current factory or supply chain efforts (a process that is sometimes referred to as leagile manufacturing). Many of the fundamental techniques that are deeply rooted within Lean thinking lend nicely towards the Agile production method, so why alter an entire process when you can build upon it?
To make a long story short: Lean and Agile are complimentary methodologies that many North American manufacturers are using strategically to gain a competitive advantage. It is important to note that the debate between the two processes doesn’t have to be an either-or scenario, as there are considerable pros and cons to both practices. A competent Factory Manager should conduct research into their own manufacturing methods to highlight ways that both lean and agile can work for their facility.
What originally started in the world of software development as a way to keep up with ever-changing customer needs and irregular product development cycles, Agile manufacturing has recently become a go to method for product design and development processing. The topical debate between Agile and Lean production methods has taken on a greater importance to North American manufacturers, as many industry experts have been begging the question of whether or not Agile production methods can truly be seen as an evolutionary step forward for production processing.
It is easy to understand why the agile manufacturing process may be appealing to some companies: it gives you an advantage when dealing with customer requirements, while giving you a competitive edge in an ever-evolving marketplace.
Agile methodologies can be viewed as an alternative to sequential design processes, providing manufacturers with the ability to act quickly upon unforeseen events and customer demands. With a successful Agile strategy, companies can become more dynamic, adding increased product variations and shorted lead-times.
On paper agile manufacturing sounds like a no brainer for consumer-driven manufacturing facilities, but what goes into making a facility like this run smoothly?
There are four key elements to agile manufacturing, all of which, will peak the curiosity of any Lean enthusiast:
- The product you are manufacturing has to be designed from the ground up to be modular. To be more specific, the product has to be easily manipulated early on in the production process to ensure you’re producing the most accessible product you can.
- Highly effective information technology must be implemented across all levels of your production facility. Agile manufacturing relies heavily upon I.T. automation as it facilitates a quick means of communication that can be spread across the floor.
- In an effort to improve lead times on raw materials, establishing a sound relationship with your corporate partners plays a critical role in Agile manufacturing, as small batches of components may be needed and requirements change often.
- Employers must invest time and resources into building a knowledgeable culture amongst their staff. The goal is to have employees that are extremely familiar with all the processes in your factory; so in the case that your production facility were to undergo a rapid change or adaptation, there would be minimal difficulty resetting procedures.
So perhaps rather than looking at Agile methodologies as a different way for production facilities to implement rigorous change, factory managers should begin taking queues from the Agile process in an effort to evolve their current factory or supply chain efforts (a process that is sometimes referred to as leagile manufacturing). Many of the fundamental techniques that are deeply rooted within Lean thinking lend nicely towards the Agile production method, so why alter an entire process when you can build upon it?
To make a long story short: Lean and Agile are complimentary methodologies that many North American manufacturers are using strategically to gain a competitive advantage. It is important to note that the debate between the two processes doesn’t have to be an either-or scenario, as there are considerable pros and cons to both practices. A competent Factory Manager should conduct research into their own manufacturing methods to highlight ways that both lean and agile can work for their facility.
Categories:Factory and Production