Magnatag InSight
The whiteboard and how it helps us brainstorm, innovate, motivate and create
Recent Blog Posts
Welcome to the Magnatag Whiteboards Blog
How Do You Design a Hybrid Workplace?
Fri Aug 5 2022How do you design a hybrid workplace? Better yet, how do you create an office space that invites your employees to reengage with in-person meetings while still providing the support and flexibility of a work-from-home schedule? It’s a question thousands of offices have asked since remote work became the norm, but few have been able to answer.
It’s no secret that companies want their employees back in the workplace. Since the start of the remote work revolution, dozens of studies have shown that in-person interactions are proven to enhance cooperation and communication among groups. However, many people have grown accustomed to the many luxuries of remote work, and the thought of leaving their remote lifestyle behind has become a nonstarter for even the most loyal employees.
The key to designing a hybrid office, according to Jack Cline, President of Lost Angles-based commercial real estate brokerage Lee & Associates, starts by cultivating an atmosphere and creating a group space. “Designing an open office space concept coupled with amenities and a workplace that provides an experience of value will help employees feel more welcome.” Companies can do their best to provide employees with free lunches and top-of-the-line coffee, but if that’s all the office has to offer, many workers will opt to skip the daily commute and remain remote. Instead, as Jack suggests, the key to building a successful hybrid office is to offer your employees tangible, practical benefits that can’t be found over a one-on-one zoom and never-ending email chains.
If you’ve spent any amount of time texting with a large group of friends, you know how easy it is to get locked into a conversation. When you’re in the thick of it, you’re laughing at inside jokes, reacting to hot gossip, making plans, and engaging in thought-provoking conversation all at once. It can be equal parts intoxicating and distracting, but it’s these interactions that help maintain and build friendships over time and distance.
The same principle applies to the workplace. The tiny micro-conversations that happen at the coffee machine are what bridge the gap between being known as the new guy in accounting to becoming a trusted collaborator. These are the conversations that happen outside your group of team members and spread out across departments. It’s a part of the workday that The Atlantic’s Derek Thomson refers to as soft-work. Soft-work doesn’t have to be limited to discussing your plans for the weekend; soft-work can be mentoring a new hire or learning about a different project that someone else in your company is struggling with. The point of these interactions is to build long-lasting relationships that enhance and encourage collaboration across departments and teams. A hybrid office needs to provide employees with an opportunity to engage in soft-work while simultaneously avoiding the rigid nature of the office cubicle.
According to Architectural Draftsman at AC Design Solutions Zaeem Chaudhary, a hybrid office plan must go beyond the simple open-concept large desk design if they wish to create an atmosphere that encourages this soft-work dynamic while still offering the flexibility and privacy of the work-from-home lifestyle.
“As work becomes more hybrid, office spaces will need to have a flexible design. Meeting rooms should resemble open areas that can be closed off with adjustable barriers to promote more adaptable cooperation on the go. On the other hand, hybrid offices also require more private enclosed spaces to better resemble the at-home working experience and please employees.”
What Zaeem is really talking about is the concept of multifunctional design. It’s something every remote worker is familiar with. The kitchen that doubles as an office; the fireplace mantle that serves as a backdrop for presentations; everyone that works from home understands the importance of having a flexible workspace. If remote workers can transform their living space into a functional office, there’s no reason companies can’t follow suit when it comes to retooling their offices. Offices need to comfortably sit anywhere from one to ten people; board rooms need to have furniture that can be configured differently depending on the size of the team. The more flexibility, the better! That’s why products like whiteboard walls are such a popular choice for hybrid workspaces.
While the future of the workplace will continue to evolve, there’s no denying the growing popularity of the hybrid workplace. Employees will continue to work from home, and employers will continue to yearn for the days of in-office work. However, by providing employees with an office layout that encourages cross-department collaboration and private workstations, employees will continue to make their way into the office in search of an experience that can’t be replicated on a screen or phone call.
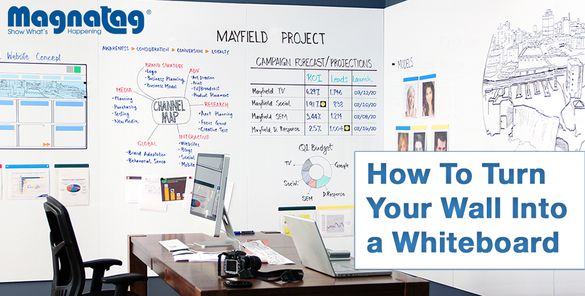
How To Turn Your Wall Into a Whiteboard
Tue Aug 3 2021Whiteboard walls are the truest form of unfiltered expression. There’s no barrier to entry; if you have an idea, you can write it on the wall. It’s that simple. However, turning a wall into a whiteboard is a more daunting task than the internet would have you believe. If you’re going the DIY method, you’ll need to follow these steps to turn your wall into a whiteboard:
- Strip paint
- Repair drywall to create a smooth surface (sand)
- Apply primer to the wall
- Depending on which route you choose to take, you’ll need to apply either an industrial adhesive to stick a laminate sheet on the wall or apply specialty paint to actually provide the wall with dry-erase properties.
Commercial-grade whiteboard walls are usually designed using a series of steel-backed panels that mount directly to the wall, providing an element of durability and magnetism that you cannot find in traditional DIY whiteboard walls. Over the past few years, the whiteboard wall panel space has diversified, incorporating dozens of material options to choose from, the most common of which include painted-steel, porcelain, and glass surfaces.
Before deciding on a whiteboard wall panel, you need to keep in mind that professional installers are typically billed at an hourly rate. A whiteboard wall installation can range anywhere from 30-minutes to days depending on the number of walls and classification of whiteboard panels in play. For instance, whiteboard wall panels that designate specific left and right-end panels require installers to fully layout and map exact panel locations prior to installation. In contrast, wall panels without designations can be installed in any order, directly out of the box. Alternatively, whiteboard wall panels that use splines and mounting trim will require installers to make cuts and modifications to the material prior to the install. While these modifications and requirements may only seem like minor pain points, multiplying these requirements across dozens of walls and panels can quickly amount to hours of additional labor costs.
At Magnatag, we've developed a line of magnetic whiteboard wall panels that streamline the installation process to make it fast, simple, and secure while maintaining a durable writing surface. Our line of WhiteWall® dry-erase wall panels utilize a patented mounting bracket system that can be installed in a matter of minutes with the help of a power drill, level, and a few additional hands. All that's required for installation is to mount the brackets onto the wall and slide panels into their designated position—it's that simple. Since WhiteWall panels are designed with precision-formed self-edges, you can create a smooth, uninterrupted writing surface without the need to specify end panels or modify mounting brackets. We also manufacture WhiteWalls using our proprietary porcelain-like Magnalux® dry-erase surface. Magnalux is a painted enamel surface is evenly applied to steel that will not stain, crack or fade after years of daily use.
Before you start looking into turning your wall into a whiteboard, it's important to be mindful of the two primary elements that go into a successful whiteboard wall transformation: ease of installation and durability. While cost-effective, DIY whiteboard wall transformations can take hours to prep and fail to provide the long-lasting durability found in commercial whiteboard wall panels. Commercial-grade whiteboard wall panels that rely on splines and mounting trim can take hours to install, and in turn, increase labor costs. Magnatag WhiteWall magnetic dry-erase whiteboard wall panels combine the best properties of commercial whiteboard wall panels with a simple installation process that you can complete in minutes. If you're in the market to transform your wall into a creative hotspot, Magnatag is the best place to start your journey.
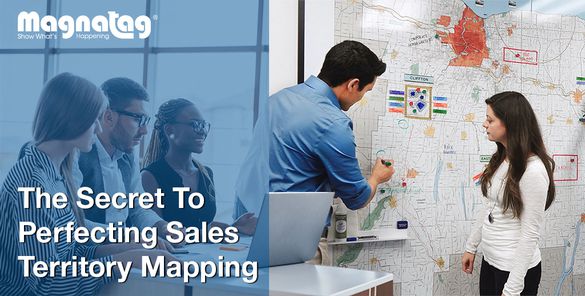
The Secret To Perfecting Sales Territory Mapping
Wed Apr 29 2020It’s estimated that somewhere around 65% of all small businesses in the U.S. close within their first ten years of operation. Of course, there are thousands of companies across the county that remain stable and profitable well beyond the ten-year mark. So what’s the secret that’s kept the remaining 45% afloat? “We focus on feedback,” says Jen Moon, Marketing Manager at Kaput Products. Kaput recently celebrated their 20th year in the pest control industry and continue to show signs of growth after two decades of operation.
The company’s business model runs through a diverse network of distributors and dealers that serve a specific territory. Customers looking to take care of a pest infestation must go directly through their local dealer to acquire any of Kaput’s products. If there’s no local dealer available, aspiring pest-exterminators in the making are encouraged to reach out to the company directly, highlighting potential gaps in the company’s distribution model. New territories are added to their distribution map regularly thanks to contributions from their traveling sales team and user feedback loop.
Part of Jen’s responsibilities at Kaput involve tracking, managing, and updating the company’s regional map as it evolves throughout the business year. Up until a few months ago, the entirety of the company’s distribution and travel data was only logged online, which was fine. Kaput’s database was still regularly updated, sales team members were still visiting new prospects, and the company was still discovering new territorial expansion opportunities; the only issue was that the software wasn’t easily accessible for quick reference points. “If I want to look something up as a quick reference, I want it to be easy to access,” Jen explained.
A few months ago, Jen reached out to the team at Magnatag Visible Systems to find an easy to access tool for managing Kaput’s territorial map. The solution: a large format, full color, magnetic dry-erase map of the United States. Standing eight feet wide and over five feet tall, the map is designed to outline individual cities and their corresponding counties, making it the perfect tool for identifying gaps in Kaput’s distribution strategy.
“We ordered our map alongside some of the colored magnets to use for marking territories for our dealers and distributors. We use one color to mark the distributors that currently carry our baits and another color to represent potential dealers… We also use a separate color to identify pests that are commonly associated with a specific location. Using this as a big picture, I can fill in the gaps in our marketing program as needed.”
Today, Jen and the rest of the Kaput team use the digital software and physical dry-erase map in tandem, with each tool serving its own purpose; the software logs and archives their regional dealer information while the map visualizes opportunities in their distribution network at a glance.
For over fifty years, Magnatag Visible Systems has developed high-quality printed magnetic dry-erase boards. If you’re looking to bring a personal and motivational approach to your project management strategy, contact us at sales@magnatag.com or give us a call at (800) 624-4154.