Magnatag InSight
The whiteboard and how it helps us brainstorm, innovate, motivate and create
Factory and Production
Blog posts that relate to news in the factory and production fields or case studies conducted with our factory and production customers.
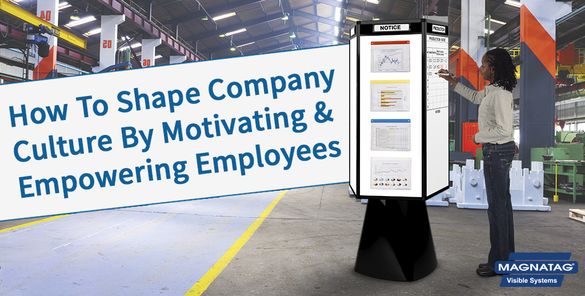
How Tapecon Shaped Company Culture By Motivating & Empowering Employees
Fri Aug 3 2018By: Mike P
According to an article published in the Harvard Business Review, an estimated 75% of B2B customers rely on word of mouth when making purchasing decisions. For OEM manufacturers like Tapecon Inc, this means nothing is more important than focusing on quality in their production efforts. Located in Buffalo NY, Tapecon’s 90,000 square foot factory specializes in manufacturing prototypes, components, assemblies, and full production services involving custom materials converting and specialized printing.
Over the past few years, the company has made significant strides to improve quality in their factory by executing a “huge push” for culture improvement. The idea behind this movement—as described by Tapecon Supply Chain Manager, Greg Davis— was to “reinforce the company’s core values [which are]: learning is a lifestyle, embrace the challenge, improve it, and collect and collaborate.” Each value is designed to play a part in building a factory centered around continuous improvement and innovation. For these values to have a significant impact on Tapecon’s production efforts, employees need to be able to embrace and own the company’s core values.
Every week, the facility holds mandatory meetings for all employees to review SQDC metrics and partake in peer nominations. With each meeting totaling somewhere around 15 minutes, the goal is to address how employees are using the company’s core values to enhance production. If someone notices a co-worker exemplifying one of the company’s core values, they’re encouraged to nominate that person as a “culture champion.” A “culture champion,” as defined by Davis, is “someone that actively demonstrates our core beliefs, setting an example for others to follow.”
Before a few months ago, Tapecon held their meetings in front of a large whiteboard—which worked well; the company had a single, dedicated space to conduct their meetings. The only issue with using the wall-mounted whiteboard as a tool for peer-to-peer nominations was that the board was not accessible. To nominate a co-worker, operators had to leave their machines and walk across the factory to write on the board.
In an effort to make sure employees were able to nominate their co-workers without losing productivity, Tapecon reached out to Magnatag Visible Systems. After speaking with a Visual Systems Specialist, —a name Magnatag uses to refer to their team of product knowledge experts—Greg and the rest of his team found a solution: Magnatag’s RotoCube® Bulletin Towers. Designed as a way to take information off the wall, the RotoCube condenses a 4’ x 6’ whiteboard into a 31” footprint using its unique 5-sided design. The dry-erase tower rotates with the touch of a finger and can fit in virtually any space.
With RotoCube now fully integrated into Tapecon’s culture improvement initiative, Greg and the rest of his team have been able to improve employee morale without jeopardizing production efforts. “We have the RotoCubes right on the floor, so anyone can walk right up to the board and submit a “culture champion” nomination. We use the other remaining four sides of the tower to address elements of our SQDC process and keep everyone aware of how we’re performing. We’ve been able to save a ton of space and avoid overcrowding on the floor with the RotoCubes.” With the wall-mounted board no longer needed for meetings, the Tapecon team has repurposed the surface to work as a root-cause analysis system and further develop a culture that prioritizes innovation and continuous improvement.
Over the past few years, the company has made significant strides to improve quality in their factory by executing a “huge push” for culture improvement. The idea behind this movement—as described by Tapecon Supply Chain Manager, Greg Davis— was to “reinforce the company’s core values [which are]: learning is a lifestyle, embrace the challenge, improve it, and collect and collaborate.” Each value is designed to play a part in building a factory centered around continuous improvement and innovation. For these values to have a significant impact on Tapecon’s production efforts, employees need to be able to embrace and own the company’s core values.
Every week, the facility holds mandatory meetings for all employees to review SQDC metrics and partake in peer nominations. With each meeting totaling somewhere around 15 minutes, the goal is to address how employees are using the company’s core values to enhance production. If someone notices a co-worker exemplifying one of the company’s core values, they’re encouraged to nominate that person as a “culture champion.” A “culture champion,” as defined by Davis, is “someone that actively demonstrates our core beliefs, setting an example for others to follow.”
Before a few months ago, Tapecon held their meetings in front of a large whiteboard—which worked well; the company had a single, dedicated space to conduct their meetings. The only issue with using the wall-mounted whiteboard as a tool for peer-to-peer nominations was that the board was not accessible. To nominate a co-worker, operators had to leave their machines and walk across the factory to write on the board.
In an effort to make sure employees were able to nominate their co-workers without losing productivity, Tapecon reached out to Magnatag Visible Systems. After speaking with a Visual Systems Specialist, —a name Magnatag uses to refer to their team of product knowledge experts—Greg and the rest of his team found a solution: Magnatag’s RotoCube® Bulletin Towers. Designed as a way to take information off the wall, the RotoCube condenses a 4’ x 6’ whiteboard into a 31” footprint using its unique 5-sided design. The dry-erase tower rotates with the touch of a finger and can fit in virtually any space.
With RotoCube now fully integrated into Tapecon’s culture improvement initiative, Greg and the rest of his team have been able to improve employee morale without jeopardizing production efforts. “We have the RotoCubes right on the floor, so anyone can walk right up to the board and submit a “culture champion” nomination. We use the other remaining four sides of the tower to address elements of our SQDC process and keep everyone aware of how we’re performing. We’ve been able to save a ton of space and avoid overcrowding on the floor with the RotoCubes.” With the wall-mounted board no longer needed for meetings, the Tapecon team has repurposed the surface to work as a root-cause analysis system and further develop a culture that prioritizes innovation and continuous improvement.
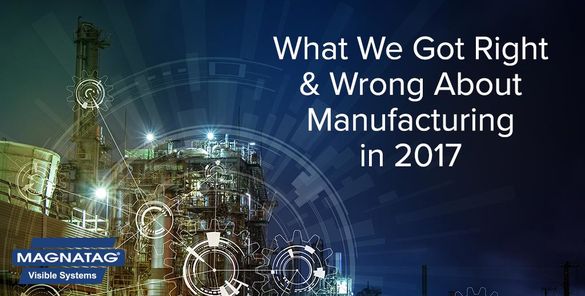
What We Got Right & Wrong About Manufacturing In 2017
Tue Jan 2 2018By: Mike P
Last year we made a few predictions about what was in store for the manufacturing industry in 2017. As the year draws to a close, we thought it would be interesting to revisit our predictions and see what we got right—and wrong—about manufacturing in the New Year.
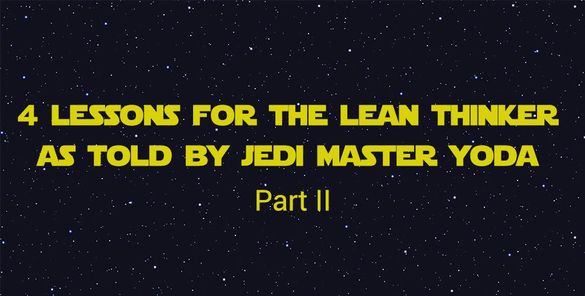
4 Lessons For The Lean Thinker As Told By Jedi Master Yoda Part 2
Thu Dec 14 2017By: Mike P
Not long ago, in this galaxy, we wrote a blog post sharing some words of advice for the lean manufacturer as told by everyone’s favorite 900-year old little green goblin-looking humanoid, Yoda. With the newest chapter in the Star Wars Saga, The Last Jedi, hitting theaters this Friday, we thought it’d be fitting to once again revisit some of Yoda’s philosophical teachings and see how they can enhance the lean thinker’s quest to reach True North.
“Much to learn you still have, my old padawan.” … “This is just the beginning!”
Everyone that’s even remotely involved with the manufacturing industry understands the importance of Toyota, the Toyoda family, and their relationship with lean. When you really think about it, the Toyoda family and the Jedi Knights aren’t all that different: both have spent a lifetime perfecting their art; they’ve been molded by their experiences—some would argue that they embody their craft—and have been made all the wiser in doing so. A few months ago, the current President of the Toyota Motor Corporation, Akio Toyoda, sent out an open letter to address the standing of the company after the financial crisis. After detailing the company’s missteps in recent years and presenting a few course-corrections the company will take in the future, Toyoda took ownership of his responsibility to lead the company in the proper direction. The letter ends with Toyoda listing a few philosophies he believes in and will keep in mind for the company’s future, one of which, bears a striking resemblance to the above quote from the wise Jedi Master: “I believe there is no “best,” only “better.” Continuous improvement is a fundamental component of lean, and one that is far too often ignored or swept to the side. It’s easy to become complacent once you’ve made improvements, but if you’re serious about lean, you must continue to innovate and problem solve. Much like the path to becoming a Jedi Master, the path to becoming a Kaizen master never truly stops.
“Fear is the path to the dark side. Fear leads to anger. Anger leads to hate. Hate leads to suffering.”
It’s safe to assume that your quest for true north doesn’t involve facing off against an evil empire, a wrinkly old man that projects lightning bolts from his fingers, or a mysterious bounty hunter, but that’s not to say that developing a lean program is not without its own set of obstacles. One of the most common obstacles lean startups face is a lack of support from executives. It’s not uncommon to hear that a lean initiative or startup failed to get off the ground due to a lack of engagement or support from an organization’s highest-ranking officers. To put it simply, many executives don’t understand the value of a lean transformation; they think of it as a cost-cutting, corner-rounding, activity. Lean leaders need to identify executive fear prior to a transformation and alleviate any hesitations that may sway executive leadership. The only “dark-side” to a lean transformation is failing to see the light at the end of the tunnel.
“I cannot teach him. The boy has no patience.”
Luke didn’t become a Jedi overnight; it wasn’t until he fell flat on his face, that he was able to understand the critical role patience plays in the path to becoming one with the force—developing lean is no different. A Kaizen culture cannot be developed in a matter of days, weeks, or months. Your organization needs to understand that developing lean takes time. Sure, you may find pockets of success within a month, but in order to see a long-lasting culture change, you need to be in it for the long haul.
“If you end your training now — if you choose the quick and easy path as Vader did — you will become an agent of evil.”
The entirety of the Star Wars series—up until this point—has revolved around the Skywalker family’s struggle to grapple with the powers of good and evil. While Luke was able to persevere through his Jedi training and become a poster child for the galaxy’s greater-good, the same cannot be said for his father. Anakin’s journey to the dark side and eventual transformation into Vader symbolizes the sensitive relationship between difficult life choices and their impact on the future. Yoda’s warning to Luke alludes to this relationship—and better yet—to the lean transformation process perfectly: Anytime an organization jumps ship and abandons their lean program, they’re inviting the three evils of manufacturing (Muda, Mura, and Muri) to creep their way back into day-to-day operations. Aborting a lean program midway through its development does nothing more than reinforce the exact behavior you initially set out to correct.
“Much to learn you still have, my old padawan.” … “This is just the beginning!”
Everyone that’s even remotely involved with the manufacturing industry understands the importance of Toyota, the Toyoda family, and their relationship with lean. When you really think about it, the Toyoda family and the Jedi Knights aren’t all that different: both have spent a lifetime perfecting their art; they’ve been molded by their experiences—some would argue that they embody their craft—and have been made all the wiser in doing so. A few months ago, the current President of the Toyota Motor Corporation, Akio Toyoda, sent out an open letter to address the standing of the company after the financial crisis. After detailing the company’s missteps in recent years and presenting a few course-corrections the company will take in the future, Toyoda took ownership of his responsibility to lead the company in the proper direction. The letter ends with Toyoda listing a few philosophies he believes in and will keep in mind for the company’s future, one of which, bears a striking resemblance to the above quote from the wise Jedi Master: “I believe there is no “best,” only “better.” Continuous improvement is a fundamental component of lean, and one that is far too often ignored or swept to the side. It’s easy to become complacent once you’ve made improvements, but if you’re serious about lean, you must continue to innovate and problem solve. Much like the path to becoming a Jedi Master, the path to becoming a Kaizen master never truly stops.
“Fear is the path to the dark side. Fear leads to anger. Anger leads to hate. Hate leads to suffering.”
It’s safe to assume that your quest for true north doesn’t involve facing off against an evil empire, a wrinkly old man that projects lightning bolts from his fingers, or a mysterious bounty hunter, but that’s not to say that developing a lean program is not without its own set of obstacles. One of the most common obstacles lean startups face is a lack of support from executives. It’s not uncommon to hear that a lean initiative or startup failed to get off the ground due to a lack of engagement or support from an organization’s highest-ranking officers. To put it simply, many executives don’t understand the value of a lean transformation; they think of it as a cost-cutting, corner-rounding, activity. Lean leaders need to identify executive fear prior to a transformation and alleviate any hesitations that may sway executive leadership. The only “dark-side” to a lean transformation is failing to see the light at the end of the tunnel.
“I cannot teach him. The boy has no patience.”
Luke didn’t become a Jedi overnight; it wasn’t until he fell flat on his face, that he was able to understand the critical role patience plays in the path to becoming one with the force—developing lean is no different. A Kaizen culture cannot be developed in a matter of days, weeks, or months. Your organization needs to understand that developing lean takes time. Sure, you may find pockets of success within a month, but in order to see a long-lasting culture change, you need to be in it for the long haul.
“If you end your training now — if you choose the quick and easy path as Vader did — you will become an agent of evil.”
The entirety of the Star Wars series—up until this point—has revolved around the Skywalker family’s struggle to grapple with the powers of good and evil. While Luke was able to persevere through his Jedi training and become a poster child for the galaxy’s greater-good, the same cannot be said for his father. Anakin’s journey to the dark side and eventual transformation into Vader symbolizes the sensitive relationship between difficult life choices and their impact on the future. Yoda’s warning to Luke alludes to this relationship—and better yet—to the lean transformation process perfectly: Anytime an organization jumps ship and abandons their lean program, they’re inviting the three evils of manufacturing (Muda, Mura, and Muri) to creep their way back into day-to-day operations. Aborting a lean program midway through its development does nothing more than reinforce the exact behavior you initially set out to correct.